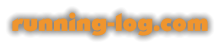
September 18, 2013 (Morning)
Exercise Type: Run
Comments:
Today was at the Caster. The melt shop was gitting ready to go on a 24 hour down day so I only saw the caster run for about 40 minutes today.
After the ladle is finished at the LMF a rail car moves it out where it is picked up by the ladle crane. It then is transported up 5 stories to the ladle cart which holds the ladel while casting is taking place. The crane sets the ladel down and then places a lid on top to limit heat loss from the melt.
The ladel is then tapped from the bottom. The steel flows out of this tap hole into a vessle underneath the ladel called the tundish. The tundish has four holes in the bottom that allow 4 strands of steel to be cast at the same time. At the bottom of each of these holes in the tundish is a nossel that controls to flow of steel into each of the molds.
If the steel must be particularly free of impurities (usually this steel is for non construction applications) shrouds are used. The stream of steel is shrouded as it flows from the ladle to the tundish and from the tundish to the moulds. These shrouds are creamic and have argon pumped through them to ensure the cleanliness of the steel.
Once the steel enters the molds cooling begins. The molds are about 3 feet long. They are made of copper and have a water jacket around them to keep them from melting. There are also several probes present in the molds to measure flow rate of steel in the mold, tempearture of the steel, and flow rate of the cooling water. Typically steel is cast in these molds at a rate of 80-90 inches per minute.
Once the steel leaves the molds it has solidified around the outside. The internal section is still molten. This outer shell is very important becasue once the solidified strand leaves the bottom of the mould nothing will physically touch it until it has reached the bottom of the cooling section 5 stories below where it was cast. It will also change from an orientation perpendicular to the ground to parallel to it. The only thing that allows this to happen is the solidified outer shell of the strand.
To make sure this outer shell forms properly the cooling of the strands is carefully controlled. The first place this happens is in the mold itself. Once the steel comes out of the bottom of the mold it goes through a spray ring where it is sprayed with high pressure water. It then passes through a set of vertical spray bars that spray it again with more water. After the strands leave this spray chamber they continue to air cool as they are gradually bent in the "banana section" to their final position on sets of rollers on the ground floor.
Again this cooling is very important when forming the solidified shell. If the shell is too thick too early (the cooling rate was too fast... the water pressure was too high) the strand will not be able to make the turn through the banana section and "break out" causing the strand to fall and the imagionable large problems. If the shell is too thin (the cooling rate was too slow.. water pressure was too low) the stand will "burn through" which as the name implies occurs when the interior molten section breeches the outer shell causing molten metal to leak out. Usually this is not as large of a problem and a break out as usually only a little molten metal escapes. However this is also problamatic and leads to srcap billets.
My day was spent cleaning these various areas. Just manual labor honestly. I almost like that better becasue it's something I can do. I didn't spend a lot of time thinking I was in the way or useless. Felt pretty good to help them.